Rezistență slabă la apă, suprafață neuniformă, conținut ridicat de pulbere și lungime neuniformă?Probleme comune și măsuri de îmbunătățire în producția de furaje acvatice
În producția noastră zilnică de hrană acvatică, am întâmpinat unele probleme din diverse aspecte.Iată câteva exemple de discutat cu toată lumea, după cum urmează:
1, Formulă
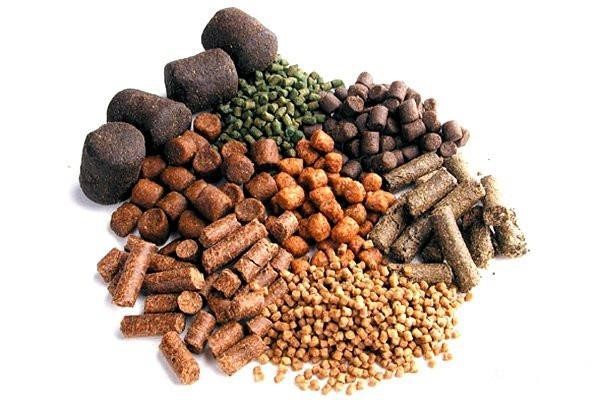
1. În structura formulei hranei pentru pești, există mai multe tipuri de materii prime de făină, cum ar fi făina de rapiță, făina de bumbac etc., care aparțin fibrei brute.Unele fabrici de ulei au tehnologie avansată, iar uleiul este practic prăjit uscat cu foarte puțin conținut.Mai mult, aceste tipuri de materii prime nu sunt ușor absorbante în producție, ceea ce are un impact foarte mare asupra granulării.În plus, făina de bumbac este greu de zdrobit, ceea ce afectează eficiența.
2. Soluție: Utilizarea prăjiturii de rapiță a fost crescută, iar în formulă au fost adăugate ingrediente locale de înaltă calitate, precum tărâțe de orez.În plus, a fost adăugat grâu, care reprezintă aproximativ 5-8% din formulă.Prin ajustare, efectul de granulație în 2009 este relativ ideal, iar randamentul pe tonă a crescut și el.Particulele de 2,5 mm sunt între 8-9 tone, o creștere de aproape 2 tone față de trecut.Aspectul particulelor s-a îmbunătățit semnificativ.
În plus, pentru a îmbunătăți eficiența zdrobirii făinii de semințe de bumbac, am amestecat făina de bumbac și făina de rapiță într-un raport de 2:1 înainte de zdrobire.După îmbunătățire, viteza de zdrobire a fost practic egală cu viteza de zdrobire a făinii de rapiță.
2, Suprafața neuniformă a particulelor
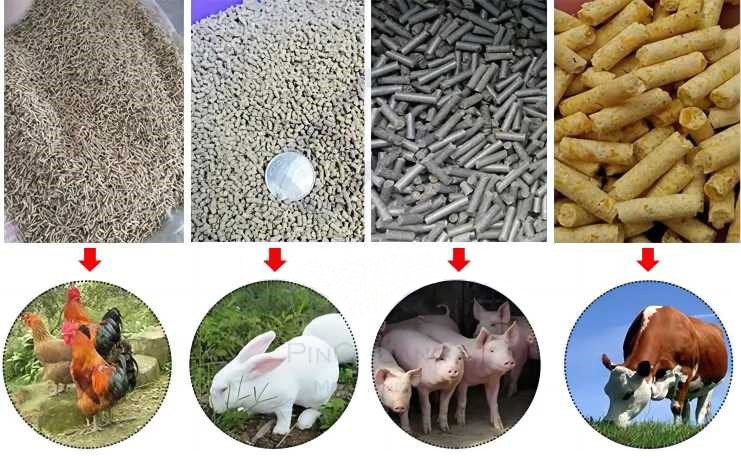
1. Are un impact mare asupra aspectului produsului finit, iar atunci când este adăugat în apă, este predispus la prăbușire și are o rată scăzută de utilizare.Motivul principal este:
(1) Materiile prime sunt zdrobite prea grosier, iar în timpul procesului de revenire, ele nu sunt complet maturate și înmuiate și nu pot fi bine combinate cu alte materii prime atunci când trec prin găurile matriței.
(2) În formula de hrană pentru pește cu un conținut ridicat de fibre brute, din cauza prezenței bulelor de abur în materia primă în timpul procesului de revenire, aceste bule se sparg din cauza diferenței de presiune dintre interiorul și exteriorul matriței în timpul comprimării particulelor, rezultând suprafața neuniformă a particulelor.
2. Măsuri de manipulare:
(1) Controlați corect procesul de zdrobire
În prezent, atunci când producem hrană pentru pești, compania noastră folosește micro pulbere de sită de 1,2 mm ca materie primă în vrac.Controlăm frecvența de utilizare a sitei și gradul de uzură al ciocanului pentru a asigura finețea zdrobirii.
(2) Controlați presiunea aburului
Conform formulei, reglați în mod rezonabil presiunea aburului în timpul producției, controlând în general aproximativ 0,2.Datorită cantității mari de materii prime din fibre grosiere din formula de hrană pentru pește, sunt necesari abur de înaltă calitate și un timp rezonabil de temperare.
3, Rezistenta slaba la apa a particulelor
1. Acest tip de problemă este cea mai frecventă în producția noastră zilnică, în general legată de următorii factori:
(1) Timpul scurt de revenire și temperatura scăzută de revenire au ca rezultat o revenire neuniformă sau insuficientă, un grad scăzut de maturare și o umiditate insuficientă.
(2) Materiale adezive insuficiente, cum ar fi amidonul.
(3) Raportul de compresie al matriței inelare este prea scăzut.
(4) Conținutul de ulei și proporția de materii prime din fibre brute din formulă sunt prea mari.
(5) Factor de mărime a particulelor de zdrobire.
2. Măsuri de manipulare:
(1) Îmbunătățiți calitatea aburului, reglați unghiul lamei regulatorului, prelungiți timpul de revenire și creșteți în mod corespunzător conținutul de umiditate al materiilor prime.
(2) Ajustați formula, creșteți în mod corespunzător materiile prime de amidon și reduceți proporția de grăsimi și fibre brute.
(3) Adăugați adeziv dacă este necesar.(pastă de bentonită pe bază de sodiu)
(4) Îmbunătățiți raportul de compresie alinel die
(5) Controlați bine finețea zdrobirii
4, Conținut excesiv de pulbere în particule
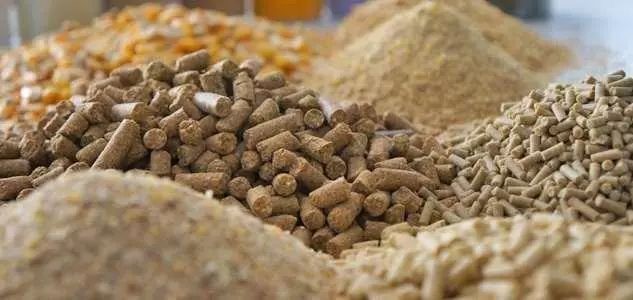
1. Este dificil să se asigure aspectul furajului general de peleți după răcire și înainte de cernere.Clienții au raportat că există mai multă cenușă fină și pulbere în peleți.Pe baza analizei de mai sus, cred că există mai multe motive pentru aceasta:
A. Suprafața particulelor nu este netedă, incizia nu este îngrijită, iar particulele sunt libere și predispuse la producția de pulbere;
B. Cerere incompletă prin ecran de clasificare, plasă de ecran înfundată, uzură severă a bilelor de cauciuc, deschidere nepotrivită a plasei ecranului etc.;
C. Există o mulțime de reziduuri fine de cenușă în depozitul de produse finite, iar clearance-ul nu este complet;
D. Există pericole ascunse în îndepărtarea prafului în timpul ambalării și cântăririi;
Măsuri de manipulare:
A. Optimizați structura formulei, selectați matrița inelală în mod rezonabil și controlați bine raportul de compresie.
B. În timpul procesului de granulare, controlați timpul de revenire, cantitatea de alimentare și temperatura de granulare pentru a coace complet și a înmuia materiile prime.
C. Asigurați-vă că secțiunea transversală a particulelor este îngrijită și utilizați un cuțit moale de tăiere din bandă de oțel.
D. Reglați și mențineți ecranul de notare și utilizați o configurație rezonabilă a ecranului.
E. Utilizarea tehnologiei secundare de screening sub depozitul de produse finite poate reduce foarte mult raportul conținutului de pulbere.
F. Este necesar să curățați depozitul de produse finite și circuitul în timp util.În plus, este necesară îmbunătățirea dispozitivului de ambalare și de îndepărtare a prafului.Cel mai bine este să utilizați presiunea negativă pentru îndepărtarea prafului, ceea ce este mai ideal.În special în timpul procesului de ambalare, lucrătorul de ambalare ar trebui să bată și să curețe în mod regulat praful din buncărul tampon al cântarului de ambalare..
5, Lungimea particulelor variază
1. În producția zilnică, întâmpinăm adesea dificultăți de control, în special pentru modelele de peste 420. Motivele pentru aceasta sunt rezumate aproximativ după cum urmează:
(1) Cantitatea de alimentare pentru granulare este neuniformă, iar efectul de temperare fluctuează foarte mult.
(2) Decalaj inconsecvent între rolele de matriță sau uzura severă a matriței inelare și a rolelor de presiune.
(3) De-a lungul direcției axiale a matriței inelare, viteza de descărcare la ambele capete este mai mică decât cea din mijloc.
(4) Orificiul de reducere a presiunii a matriței inelare este prea mare, iar viteza de deschidere este prea mare.
(5) Poziția și unghiul lamei de tăiere sunt nerezonabile.
(6) Temperatura de granulare.
(7) Tipul și înălțimea efectivă (lățimea lamei, lățimea) lamei de tăiere cu matriță inelă au un impact.
(8) În același timp, distribuția materiilor prime în interiorul camerei de compresie este neuniformă.
2. Calitatea furajelor și a peletelor este în general analizată pe baza calităților interne și externe ale acestora.Ca sistem de producție, suntem mai expuși lucrurilor legate de calitatea externă a peletelor de furaje.Din punct de vedere al producției, factorii care afectează calitatea peletelor pentru furaje acvatice pot fi rezumați după cum urmează:
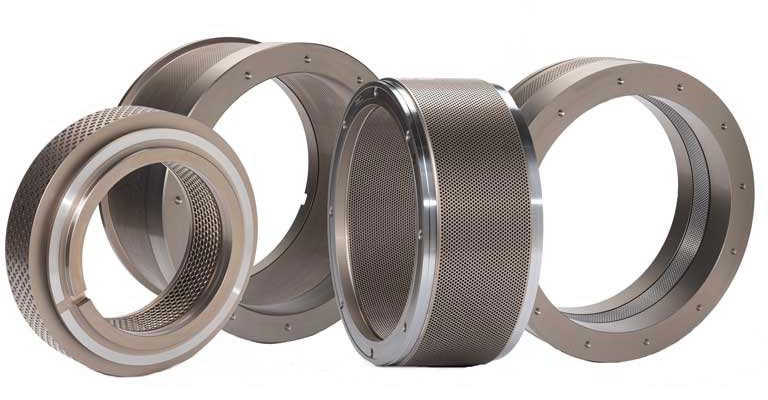
(1) Proiectarea și organizarea formulelor au un impact direct asupra calității peletelor de hrană acvatică, reprezentând aproximativ 40% din total;
(2) Intensitatea zdrobirii și uniformitatea mărimii particulelor;
(3) Diametrul, raportul de compresie și viteza liniară a matriței inelare au un impact asupra lungimii și diametrului particulelor;
(4) Raportul de compresie, viteza liniară, efectul de călire și revenire a matriței inelare și influența lamei de tăiere asupra lungimii particulelor;
(5) Conținutul de umiditate al materiilor prime, efectul de călire, răcirea și uscarea au un impact asupra conținutului de umiditate și a aspectului produselor finite;
(6) Echipamentul în sine, factorii de proces și efectele de călire și revenire au un impact asupra conținutului de pulbere de particule;
3. Măsuri de manipulare:
(1) Reglați lungimea, lățimea și unghiul racletei de material și înlocuiți racleta uzată.
(2) Acordați atenție ajustării în timp util a poziției lamei de tăiere la începutul și aproape de sfârșitul producției din cauza cantității mici de alimentare.
(3) În timpul procesului de producție, asigurați o rată stabilă de alimentare și alimentare cu abur.Dacă presiunea aburului este scăzută și temperatura nu poate crește, aceasta trebuie ajustată sau oprită în timp util.
(4) Reglați în mod rezonabil distanța dintrecarcasă cu role.Urmați noua matriță cu role noi și reparați prompt suprafața neuniformă a rolei de presiune și a matriței inelare din cauza uzurii.
(5) Reparați orificiul de ghidare al matriței inelare și curățați prompt orificiul formei blocat.
(6) La comanda matriței inelare, raportul de compresie al celor trei rânduri de găuri la ambele capete ale direcției axiale a matriței inelare originale poate fi cu 1-2 mm mai mic decât cel din mijloc.
(7) Folosiți un cuțit de tăiere moale, cu o grosime controlată între 0,5-1mm, pentru a asigura o margine ascuțită cât mai mult posibil, astfel încât să se afle pe linia de plasare dintre matrița inelară și rola de presiune.
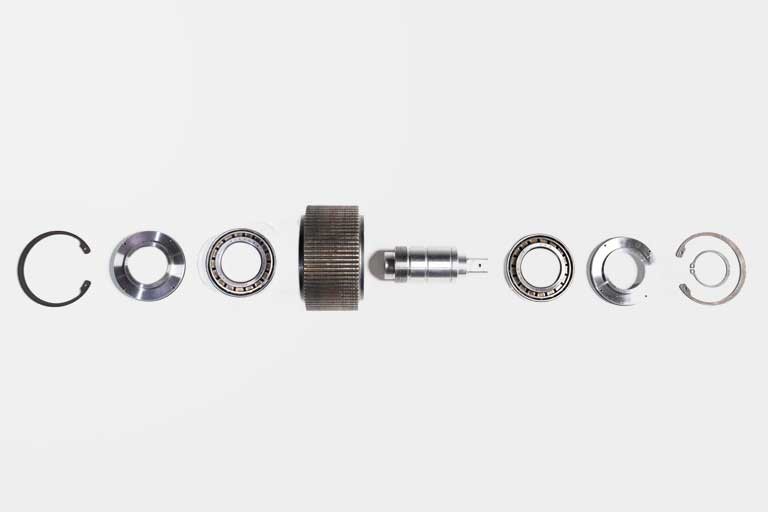
(8) Asigurați-vă concentricitatea matriței inelare, verificați în mod regulat jocul axului granulatorului și reglați-l dacă este necesar.
6, Rezumat puncte de control:
1. Măcinare: finețea măcinarii trebuie controlată în conformitate cu cerințele specificațiilor
2. Amestecare: uniformitatea amestecării materiilor prime trebuie controlată pentru a asigura cantitatea de amestecare adecvată, timpul de amestecare, conținutul de umiditate și temperatura.
3. Maturare: Presiunea, temperatura și umiditatea mașinii de umflat trebuie controlate
Dimensiunea și forma materialului particulelor: trebuie selectate specificațiile adecvate ale matrițelor de compresie și ale lamelor de tăiere.
5. Conținutul de apă al furajului finit: Este necesar să se asigure timpul și temperatura de uscare și răcire.
6. Pulverizarea uleiului: Este necesar să se controleze cantitatea precisă de ulei pulverizat, numărul de duze și calitatea uleiului.
7. Screening: Selectați dimensiunea sitei în funcție de specificațiile materialului.
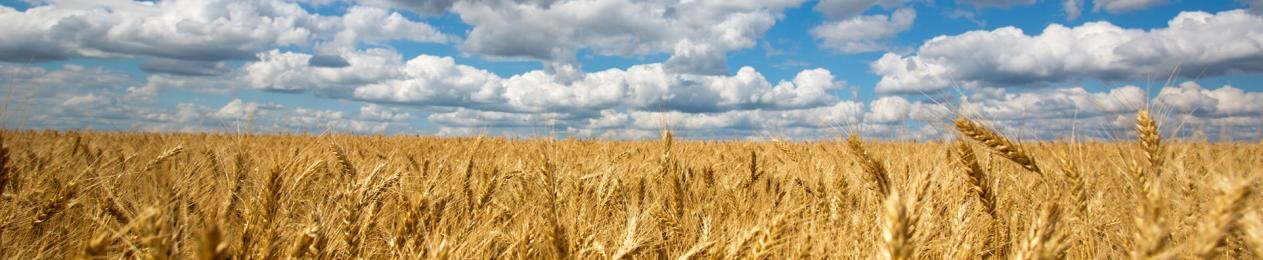
Ora postării: 30-nov-2023