În industria de granulare, fie că este vorba de o mașină de granulare cu matriță plană sau de o mașină de granulare cu matriță inelară, principiul său de funcționare este de a se baza pe mișcarea relativă dintre carcasa rolei de presiune și matriță pentru a prinde materialul și a intra în stația efectivă, a-l extruda în formă și apoi a-l tăia în particule de lungimea necesară cu lama de tăiere.
Carcasă de rolă de presă a particulelor
Carcasa rolei de presiune include în principal un arbore excentric, rulmenți, o carcasă a rolei de presiune manșonată în exteriorul arborelui rolei de presiune și componente utilizate pentru susținerea și fixarea carcasei rolei de presiune.
Carcasa rolei de presiune comprimă materialul în orificiul matriței și îl formează sub presiune în orificiul matriței. Pentru a preveni alunecarea rolei de presiune și pentru a crește forța de prindere, trebuie să existe o anumită forță de frecare între rola de presiune și material. Prin urmare, se iau adesea măsuri pentru creșterea rezistenței la frecare și la uzură la suprafața rolei de presiune. Atunci când se determină parametrii structurali ai rolei de presiune și ai matriței, forma structurală și dimensiunea suprafeței exterioare a rolei de presiune au un impact semnificativ asupra eficienței de granulare și a calității particulelor.
Structura suprafeței carcasei rolei de presiune
Există trei tipuri comune de suprafață pentru rolele de presare a particulelor existente: suprafață canelată a rolei, suprafață canelată a rolei cu etanșare la margini și suprafață de rolă tip fagure de miere.
Rola de presiune de tip canelură dințată are performanțe bune de rulare și este utilizată pe scară largă în fabricile de hrană pentru animale și păsări de curte. Cu toate acestea, din cauza alunecării furajelor în canelura dințată, uzura rolei de presiune și a matriței inelare nu este foarte uniformă, iar uzura la ambele capete ale rolei de presiune și ale matriței inelare este mai severă.
Rola de presiune de tip canelură dințată cu etanșare la margini este potrivită în principal pentru producția de materiale acvatice. Materialele acvatice sunt mai predispuse la alunecare în timpul extrudării. Datorită etanșării la margini pe ambele părți ale canelurii dințate, nu este ușor să alunece spre ambele părți în timpul extrudării alimentării, rezultând o distribuție mai uniformă a alimentării. Uzura rolei de presiune și a matriței inelare este, de asemenea, mai uniformă, rezultând o lungime mai consistentă a peletelor produse.
Avantajul rolei tip fagure este că uzura matriței inelare este uniformă, iar lungimea particulelor produse este, de asemenea, relativ constantă. Cu toate acestea, performanța bobinei este slabă, ceea ce afectează randamentul granulatorului și nu este la fel de comună ca utilizarea rolei cu fantă în producția reală.
Următorul este un rezumat al 10 tipuri de role de presiune pentru mașini de prelucrat particule pentru matrițele inelare cu role de presiune Baoshell, iar ultimele 3 sunt cu siguranță cele pe care nu le-ați văzut!
Tipul cu canelură nr. 10
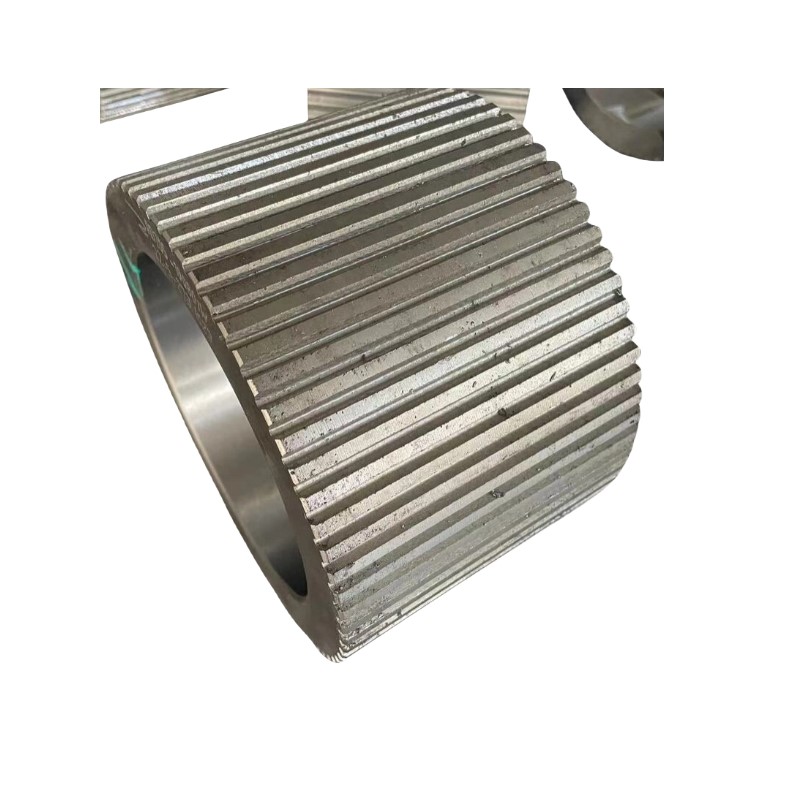
NR. 9 Tip cu canelură închisă
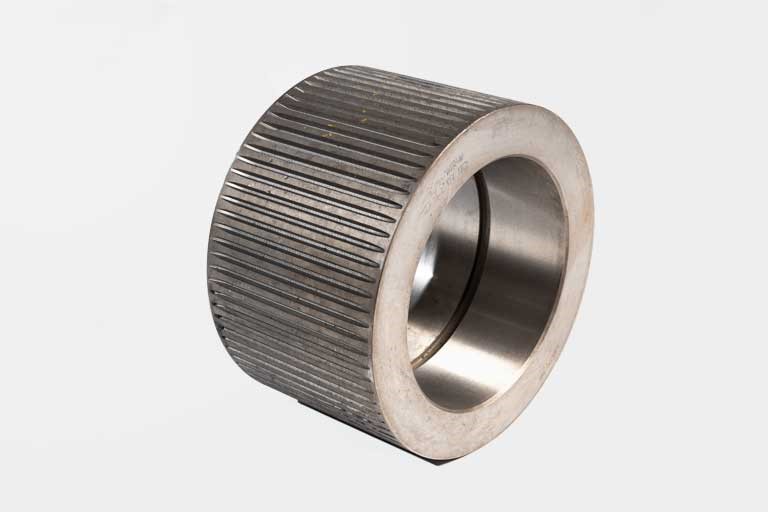
Tipul fagure de miere nr. 8
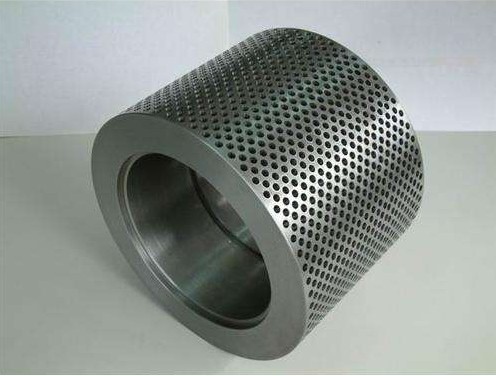
Nr. 7 În formă de diamant
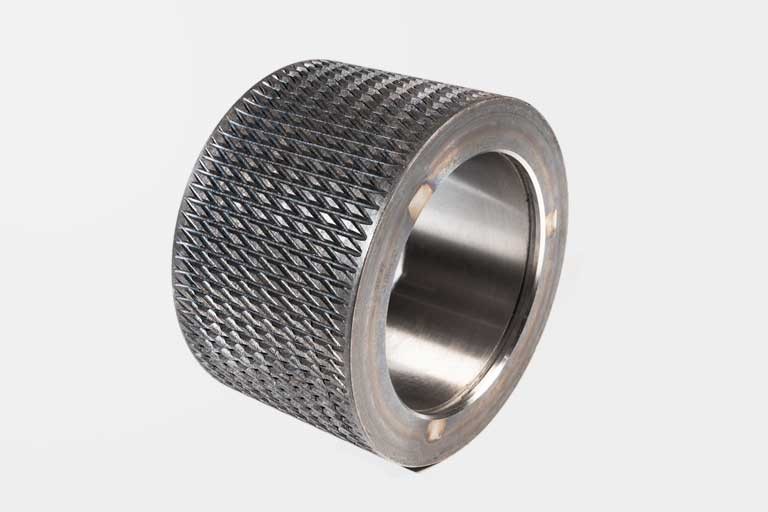
NR.6 Canelură înclinată
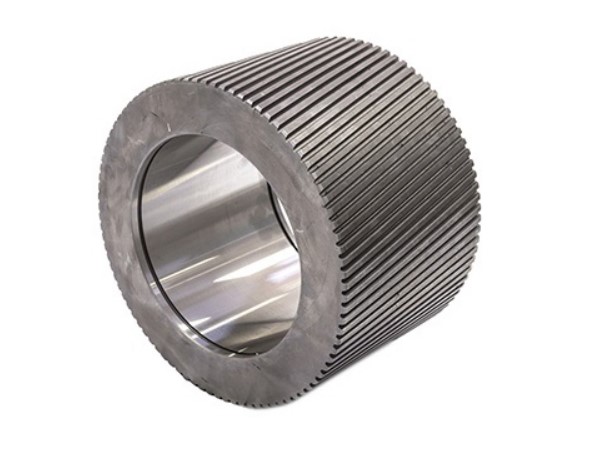
Nr. 5 Groove+fagure de miere
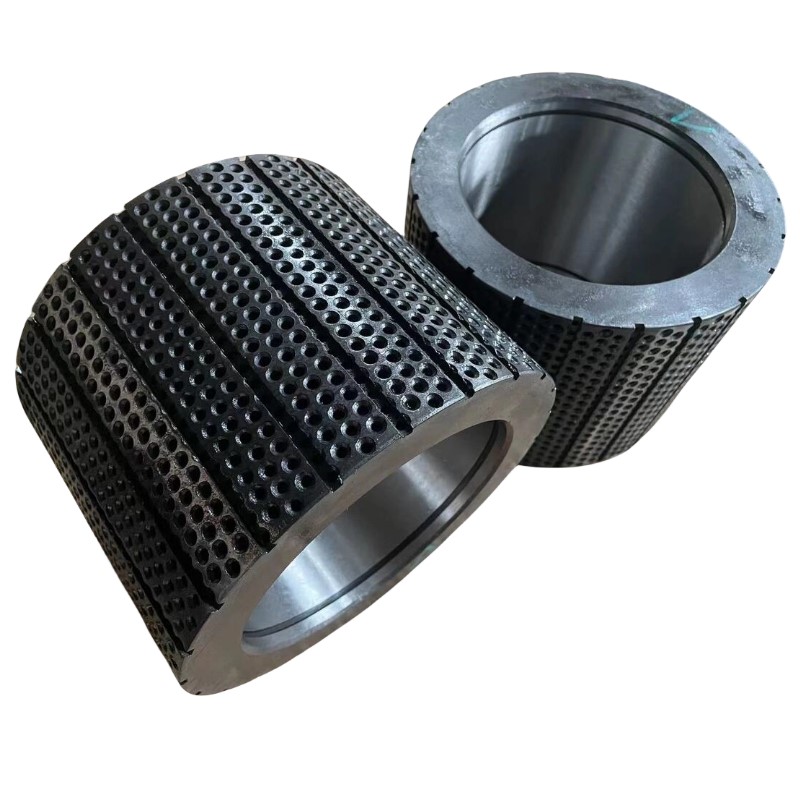
NR. 4 Canal închis + fagure de miere
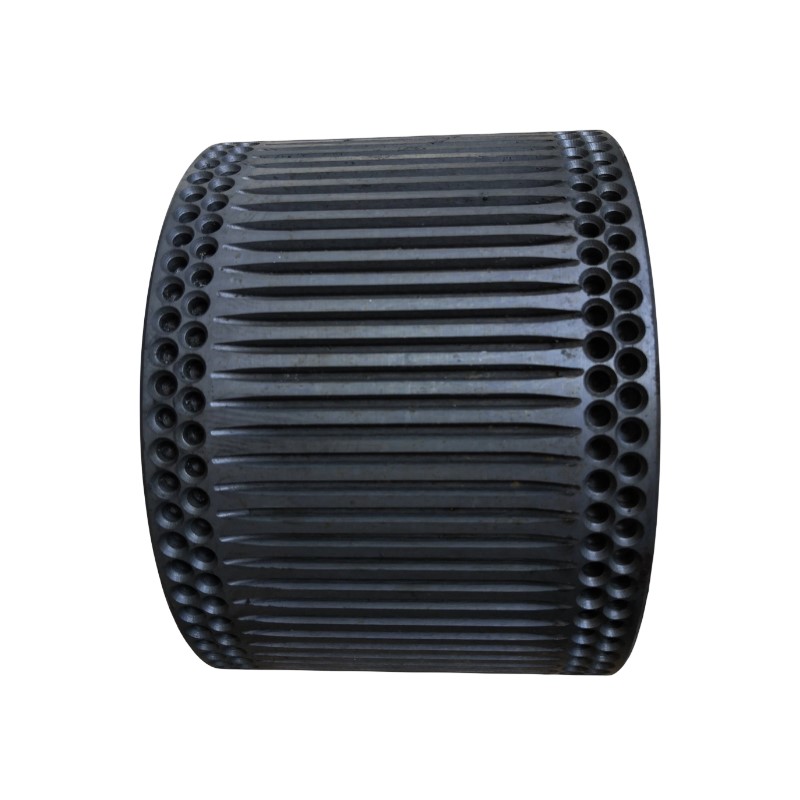
NR.3 Canelură înclinată + fagure de miere
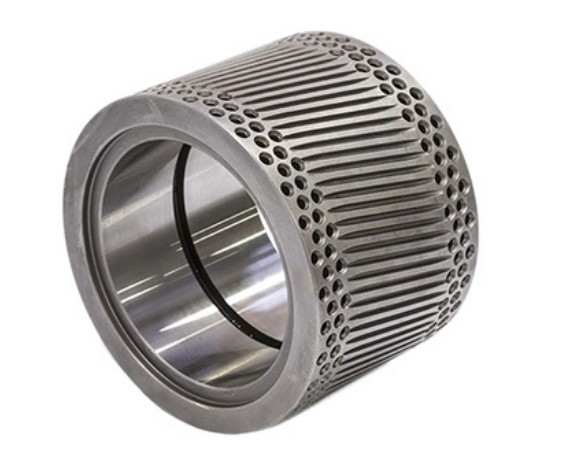
Ondulație de os de pește nr. 2
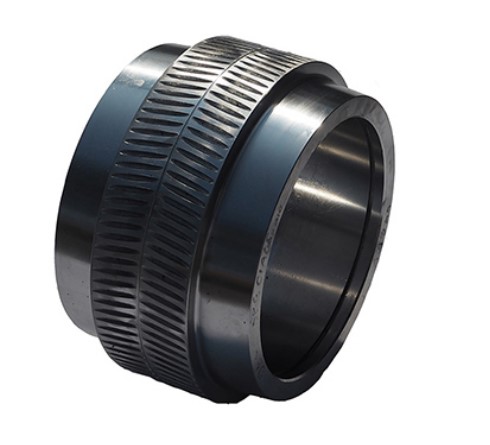
NR. 1 Ondulație în formă de arc
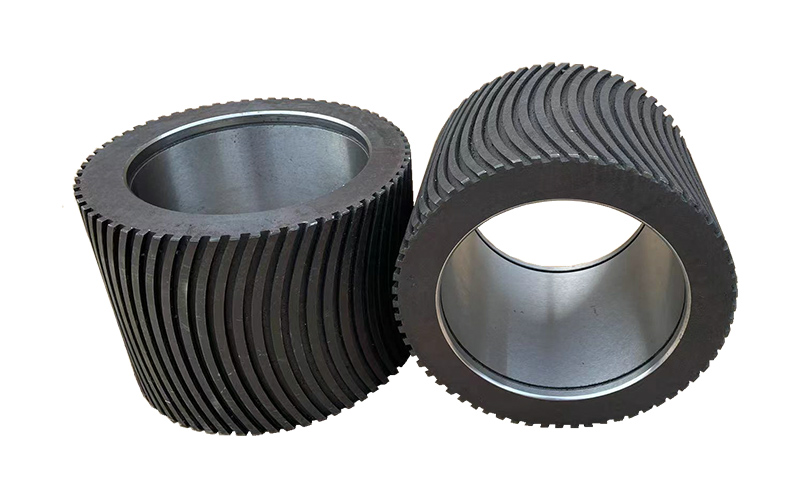
MODEL SPECIAL: CARCASĂ DE COLIER DIN CARBURĂ DE TUNGSTEN
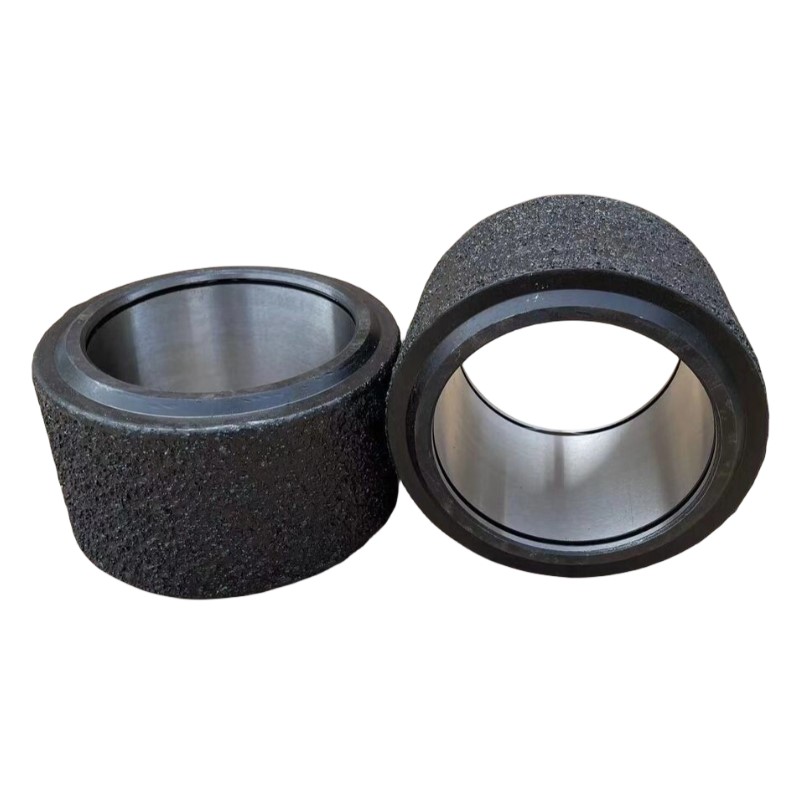
Metoda de tratament pentru alunecarea rolei de presiune a mașinii de particule
Din cauza mediului de lucru dificil, a intensității ridicate de lucru și a uzurii rapide a carcasei rolei de presiune, aceasta este o parte vulnerabilă a mașinii de granulare și trebuie înlocuită periodic. Practica de producție a arătat că, atâta timp cât caracteristicile materialelor de producție sau alte condiții se modifică în timpul procesării, poate apărea fenomenul de alunecare a rolei de presiune a mașinii de granulare. Dacă există alunecare a rolei de presiune în timpul procesului de granulare, vă rugăm să nu vă panicați. Pentru detalii specifice, vă rugăm să consultați următoarele tehnici:
Motivul 1: Concentricitate slabă a rolei de presiune și a instalării axului
Soluţie:
Verificați dacă instalarea rulmenților rolei de presiune este rezonabilă pentru a evita devierea carcasei rolei de presiune într-o parte.
Motivul 2: Gura clopotului matriței inelare este șlefuită, ceea ce face ca matrița să nu mănânce materiale
Soluţie:
Verificați uzura clemelor, a roților de transmisie și a inelelor de căptușeală ale granulatorului.
Reglați concentricitatea instalării matriței inelare, cu o eroare care să nu depășească 0,3 mm.
Distanța dintre rolele de presiune trebuie ajustată astfel încât: jumătate din suprafața de lucru a rolelor de presiune să lucreze cu matrița, iar roata de reglare a distanței și șurubul de blocare trebuie, de asemenea, asigurate că sunt în stare bună de funcționare.
Când rola de presiune patinează, nu lăsați mașina de tocat particule să funcționeze în gol pentru o perioadă lungă de timp și așteptați ca aceasta să descarce materialul singură.
Raportul de compresie al deschiderii matriței inelare utilizate este prea mare, ceea ce provoacă o rezistență ridicată la descărcarea materialului din matriță și este, de asemenea, unul dintre motivele pentru alunecarea rolei de presiune.
Mașina de peleți nu trebuie lăsată să funcționeze inutil fără alimentare cu material.
Motivul 3: Rulmentul rolei de presiune este blocat
Soluţie:
Înlocuiți rulmenții rolelor de presiune.
Motivul 4: Carcasa rolei de presiune nu este rotundă
Soluţie:
Calitatea carcasei rolei este neclasificată, înlocuiți sau reparați carcasa rolei.
Când rola de presiune patinează, aceasta trebuie oprită în timp util pentru a evita frecarea prelungită a rolei de presiune în gol.
Motivul 5: Îndoirea sau slăbirea axului rolei de presiune
Soluţie:
Înlocuiți sau strângeți axul și verificați starea axului rolei de presiune atunci când înlocuiți matrița inelară și rola de presiune.
Motivul 6: Suprafața de lucru a rolei de presiune este relativ nealiniată cu suprafața de lucru a matriței inelare (intersectarea marginilor)
Soluţie:
Verificați dacă rola de presiune este instalată incorect și înlocuiți-o.
Verificați dacă axul excentric al rolei de presiune este deformat.
Verificați dacă există uzură la rulmenții sau bucșele arborelui principal al mașinii de particule.
Motivul 7: Distanța dintre axul granulatorului este prea mare
Soluţie:
Verificați jocul de strângere al granulatorului.
Motivul 8: Rata de perforare a matriței inelare este scăzută (mai puțin de 98%)
Soluţie:
Folosește un burghiu cu pistol pentru a găuri orificiul matriței sau fierbe-l în ulei și macină-l înainte de a-l hrăni.
Motivul 9: Materiile prime sunt prea grosiere și au un conținut ridicat de umiditate
Soluţie:
Acordați atenție menținerii unui conținut de umiditate de aproximativ 15%. Dacă conținutul de umiditate al materiilor prime este prea mare, va exista blocarea matriței și alunecarea după ce materiile prime intră în matrița inelară. Intervalul de control al umidității materiilor prime este între 13-20%.
Motivul 10: Alimentarea mucegaiului nou prea rapidă
Soluţie:
Reglați viteza pentru a vă asigura că rola de presiune are o tracțiune suficientă, preveniți alunecarea rolei de presiune și verificați prompt uzura matriței inelare și a rolei de presiune.
Data publicării: 25 martie 2024